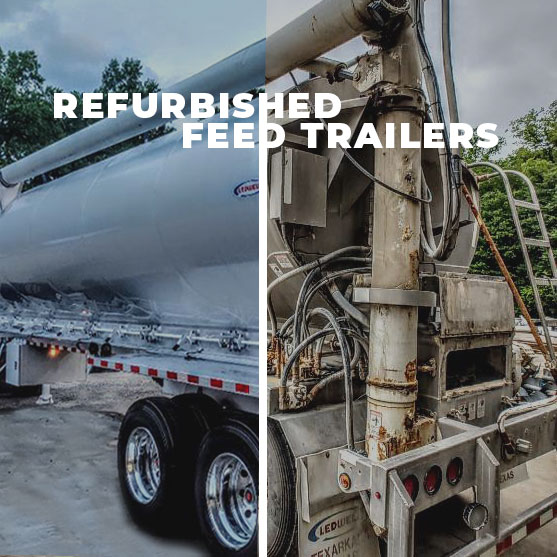
Ledwell East: A Commitment to Quality on the East Coast
Fayetteville, North Carolina, sits along the Cape Fear River in the Carolina Sandhills, a region known for its resilience—just like the hardworking folks who call it home. That same grit and determination make it the perfect place for Ledwell East, our second location, established in 2008 to provide parts and service to our East Coast customers.
What started as a parts and service center has grown into a full-scale operation, handling final manufacturing processes and refurbishing equipment. With the same high standards as our Texarkana headquarters, Ledwell East ensures every job is done right.
The Art of Refurbishing: Giving New Life to Bulk Haul Feed Trailers
When a Bulk Haul Feed Trailer rolls into the Fayetteville shop for refurbishment, our team follows a precise step-by-step process to restore it to peak condition.
1. First, it gets a proper bath.
A thorough wash strips away dirt and buildup, making it easier to evaluate what needs attention.
2. Next, our experts test every system
Hydraulics, pneumatics, and electrical components—to pinpoint any hidden issues.
3. Finally, a detailed visual inspection
Inside and out ensures that nothing is overlooked. This walk-through helps the team determine what needs repair or replacement and estimate the time required to get it back on the road.
No Job Too Big, No Trailer Too Uncommon
While feed trailers are a common sight in the Fayetteville shop, every now and then, something unfamiliar rolls through the doors. But that never slows the team down. They bring innovation and problem-solving to every project, using their expertise to tackle any challenge.
At Ledwell East, it’s not just about fixing equipment—it’s about keeping businesses moving and ensuring every customer gets the reliable, high-quality service they expect. No matter the challenge, our team rolls up their sleeves and gets the job done.
Get a Free Equipment Evaluation
Not sure what repairs you need?
Our team will inspect your equipment and provide a detailed assessment. Contact us now!