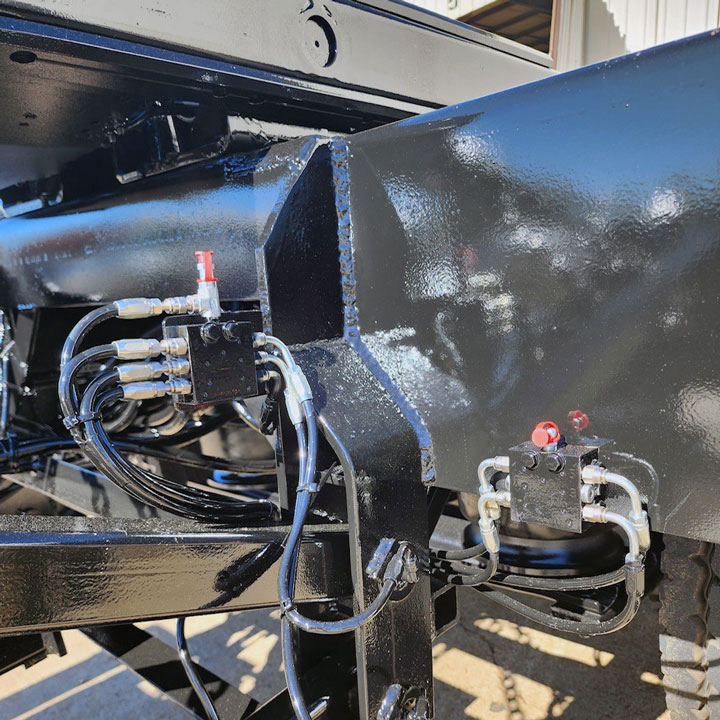
Greasing equipment is one of those essential maintenance tasks that can be easily overlooked, but skipping it can lead to big problems. At Ledwell, we’ve seen how routine greasing can extend equipment life, improve performance, and reduce downtime. That’s why our advanced grease system has made it easier than ever to maintain equipment.
Ledwell’s grease system simplifies the greasing process using just one or two centralized grease points. These points evenly distribute grease to all necessary pins and components across the unit, eliminating the need to crawl underneath or reach awkward spots to keep things running smoothly.
WHY IT MATTERS
Time-Saving:
Cut greasing time from 20 minutes to just a few.
Improved Safety:
No need to crawl under or reach tight spaces.
Better Performance:
Even grease flow reduces wear and extends equipment life.
Ease of Use:
One to two grease points simplify maintenance.
This system comes standard on all HydraTilt Trucks and Rollbacks, and it’s also available as an optional upgrade on HydraTail Trailers.
This system is more than a convenience for customers using their equipment daily in tough environments; it’s a maintenance game-changer.
Whether you’re running a fleet or managing a single unit, reducing upkeep time while improving reliability is always a win.
It’s a small investment with long-term benefits. Our team is here to help. Just reach out, and we’ll walk you through the options.